一、传统开料方式为何成为制造业的“效率黑洞”?
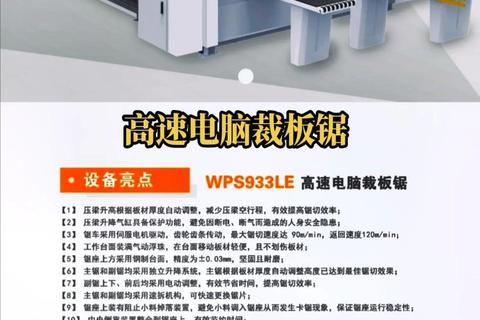
在板材加工、家具制造等重资产行业,车间里堆积如山的余料边角如同无声的控诉——据统计,传统人工开料模式下板材平均利用率仅为65%-75%。某门窗厂老板曾向笔者诉苦:“老师傅拿着计算器反复核算排版,2小时才能完成一套方案,结果切割时还是出现3%的误差。”这种依赖经验判断的作业方式,不仅造成每年数十万元的材料浪费,更让企业在订单激增时陷入产能瓶颈。当“多品种、小批量”成为市场常态,传统开料模式正遭遇前所未有的效率困局。
二、智能算法如何突破人工排版效率极限?

革新升级智能开料软件助您极致优化裁切效率的核心突破,在于将深度学习算法引入工业场景。以某上市家具企业引入的天工生产开料优化软件为例,其自主研发的NestPro 3.0算法实现了三大跨越:
1. 动态套料技术:针对600余种异形零件,通过拓扑关系分析自动生成17种排样组合,材料利用率提升至94.6%
2. 多约束条件优化:在满足纹理方向、切割间隙(±0.5mm)、设备刀具损耗等12项工艺限制下,单次计算时间从45分钟缩短至3分钟
3. 余料智能管理:建立历史余料数据库,新订单优先调用尺寸匹配的余料进行二次加工,使某橱柜企业年度余料率从8.3%降至1.7%
三、复杂生产需求下能否兼顾灵活性与精准度?
面对玻璃加工厂“每日处理200+非标订单”的挑战,钣金大师V5.0通过三大创新给出了答案:
智能图纸解析:支持DXF/DWG/CAM等8种格式文件自动识别,将设计师标注的“弧形转角R15”直接转化为切割路径,错误率从人工录入的6%降至0.2%
多目标优化模式:某电梯配件厂使用“保交付优先”模式,在材料利用率仅降低1.2%的情况下,将日均订单处理量提升40%
动态公差补偿:根据激光切割机的实时温度数据自动调整切割参数,使3mm不锈钢板的切口垂直度偏差稳定在±0.03mm以内
四、如何通过流程闭环实现全链路降本增效?
革新升级智能开料软件助您极致优化裁切效率的价值,更体现在与生产系统的深度集成:
1. 订单智能拆解:某全屋定制企业接入ERP系统后,软件自动将200㎡的整屋订单拆解为327块标准板件,并同步生成物料采购清单,备料周期从3天压缩至6小时
2. 设备协同控制:通过IoT模块直接下发G代码到数控机床,某汽车配件厂实现“排版完成即启动切割”,设备空转时间减少82%
3. 质量追溯体系:采用条码标记技术,使每块板材的原料批次、切割参数、使用工单等信息可15秒内追溯,助力某医疗器械企业通过FDA认证
五、开启智能开料新纪元的三大行动指南
1. 优先选择行业适配型软件:家具企业可关注天工软件的多层板优化模块,金属加工厂则应测试钣金大师的应力补偿算法
2. 建立动态学习机制:每月导入最新生产数据训练算法模型,某门窗厂通过持续优化使套料效率每年提升5%-8%
3. 实施分阶段数字化改造:建议从“单机版软件试用”到“MES系统对接”,最后实现“智能工厂”三级跳,避免一次性投入过大风险
革新升级智能开料软件助您极致优化裁切效率的价值已在多个行业得到验证——某家电企业引入系统后,年度材料成本降低380万元,交货周期缩短22天,更收获客户颁发的“绿色供应链标杆”奖项。当工业4.0浪潮席卷全球,智能化开料已不是选择题,而是制造业突围的必答题。
相关文章:
文章已关闭评论!